What is Zanite® Plus?
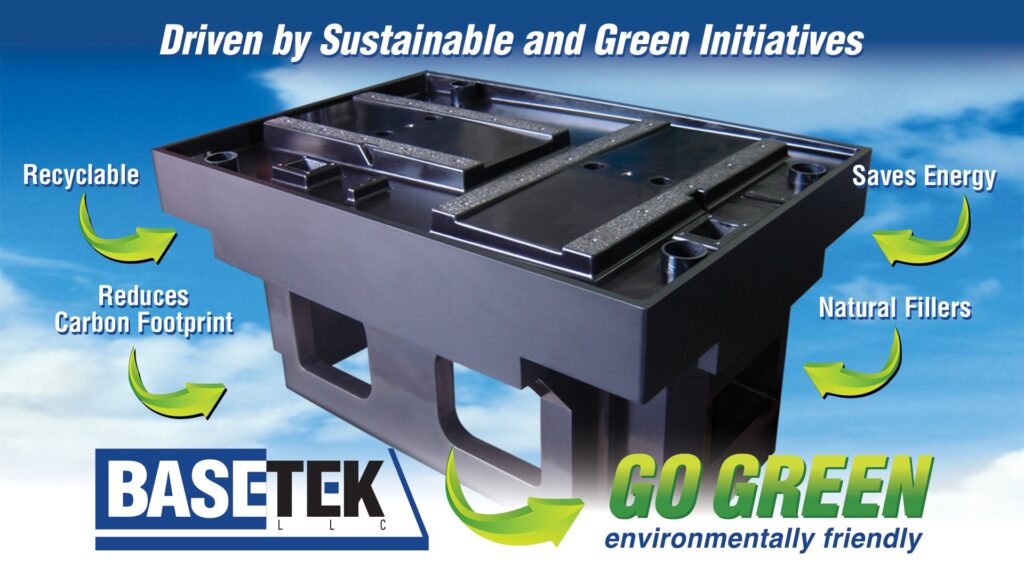
Zanite Plus mineral cast polymer composite is a blend of pure silicon dioxide ceramic (99.8%) quartz aggregate, specially formulated high strength epoxy resin and proprietary additives. The natural elliptical shape of quartz is ideal for casting intricate structures. Often this material is referred to as polymer concrete, epoxy granite, or a mineral casting.
Zanite Plus replaces traditional materials such as iron, aluminum, and steel used in the manufacture of many structural components. Castings are manufactured to tight finish tolerances that rarely required secondary operations. Our mineral cast polymer composite is accepted by design engineers throughout the world as an alternative material due to its excellent design flexibility, mechanical properties, and short production time.
Epoxy based polymer concrete castings used as machine bases originated in Europe in the mid 1970’s. The technology migrated to the USA in the early 1980’s with machine tool builders. In 2009, BaseTek, LLC purchased the technology and was assigned the legal marketing rights to the trade name Zanite from Illinois Tool Works, Inc. (ITW) Pre-cast division located in Chardon, OH.
Beginning in 2013 BaseTek began a program to study and enhance the Zanite formulation previously acquired. BaseTek utilized a combination of internal resources along with outside consultants to facilitate a reformulation of the Zanite polymer blend. Well over a year was spent evaluating each component and processing methodology.
In early 2015 we re-branded our material Zanite Plus. Through documented testing we can certify Zanite Plus polymer composite meets or exceeds the original inherited Zanite formulation in every category. BaseTek utilizes our own in-house testing equipment along with outside testing labs to verify the material properties. Specific properties are listed in the table and chart below.
Features
Industry Use
Medical
MRI scanners contain powerful magnets and their supporting structure must be non-magnetic. Traditional scanner structures are stainless steel, but Zanite Plus castings, also non-magnetic, offer a more cost-effective solution.
Metrology
Zanite Plus machines are able to withstand harsh production environments and give instant, accurate results. Zanite Plus thermal stability, design flexibility, and virtually zero moisture absorption rates help metrology equipment manufacturers achieve their goals.
Prepress
The prepress industry benefits from the high tolerances to which Zanite Plus can be cast. Precision drums are cast to 0.001″ in true cylindrical form. Zanite Plus ensures a high degree of vibration isolation, rigidity and long term dimensional stability unmatched by metal drums, internal or external. Imaging devices with Zanite Plus drums require no special climate control.
Semiconductor
Typical applications include: screen printing machines, wire and die bonding, wafer inspection and testing, lithography, laser PCB drilling machines, pick and place machines, surface profilers, wafer handling and storage, dicing machines, flip-chip, and dispensing equipment.
Pump/Rotating
Equipment
Typical applications include: non-metallic corrosion resistant baseplates for chemical and general duty process pumps and related rotating equipment such as motors and compressors. Rigid and flat (0.002” per foot) mounting surfaces speed and maintain alignment. Vibration dampening extends equipment reliability and service life.